Daily Maintenance of Liquid Packaging Machines
Daily maintenance of liquid packaging machines is a key step in ensuring smooth operation, extending the lifespan of the equipment, and maintaining production efficiency. Regular checks and simple maintenance tasks can effectively reduce machine failures and guarantee packaging quality. Below is a detailed breakdown of daily maintenance tasks for liquid packaging machines:
1. Cleaning the Machine Surface
Surface cleaning is the most basic maintenance task. It prevents dust, dirt, and liquid residue from affecting the machine’s normal operation.
Wipe the surface with a damp cloth: Use a clean damp cloth to wipe down the machine’s exterior to remove dust, dirt, or spilled liquids. Keeping the equipment clean prevents liquid accumulation and contamination, which could affect packaging quality.
Clean the filling nozzles: The filling nozzles are critical contact points with the product. Regular cleaning is essential to prevent liquid residues or contamination. It is advisable to use non-corrosive cleaning agents to avoid clogging or leaking from the filling nozzles.
Clean the control panel: Clean the dust and fingerprints from the control panel to ensure clarity and responsiveness.
2. Check Liquid Pipelines and Connectors
Liquid pipelines and connectors are essential parts of the liquid packaging machine. Any leaks, blockages, or damage could cause production delays.
Check for leaks: Inspect the liquid transport pipelines and connection joints for any signs of leakage. If a leak is found, repair or replace the affected parts immediately.
Check for blockages: Ensure the pipelines are free from any blockages. Regularly check and clean the pipelines to maintain smooth liquid flow and avoid transportation issues.
Check the connectors: Ensure all connectors are tightly secured to prevent leaks or insufficient pipeline pressure.
3. Inspect the Filling System
The filling system is the heart of the liquid packaging machine, and any issues directly affect filling accuracy and packaging efficiency.
Check for nozzle clogs: The filling nozzles may clog due to liquid residues or debris. Regularly check and clean the nozzles to keep them clear.
Check fill accuracy: Ensure the filling volume matches the preset standard. If filling is inaccurate, there may be issues with the nozzle, measurement system, or valves, which should be adjusted or repaired.
Check valve operation: Ensure that the valves open and close accurately to avoid inconsistent liquid flow or spillage.
4. Monitor the Temperature Control System
The temperature control system is critical, especially for liquids that are temperature-sensitive, such as dairy products or juices.
Check the heating system: If the equipment includes a heating system, check the heating elements to ensure they are working properly. The heating system should maintain the liquid at the desired temperature to avoid operational issues.
Check the cooling system: If the machine has a cooling function, verify that the cooling pipes are not blocked and the cooling system is functioning well to prevent overheating.
Check temperature sensors: Inspect the temperature sensors to ensure they are accurately measuring the liquid’s temperature. If temperature deviations are detected, adjustments should be made.
5. Inspect Fasteners
The fasteners, such as screws and nuts, ensure the machine remains stable and secure. Loose fasteners can affect the machine’s accuracy and safety.
Check fasteners for tightness: Regularly inspect screws and nuts on various parts of the machine (such as the filling head, drive system, etc.) to ensure they are tightened. Tighten any loose fasteners.
Check frame and supports: Inspect the machine's framework and support structures to ensure they are secure and undamaged.
6. Lubricate Moving Parts
Moving components, such as belts, gears, and bearings, require regular lubrication to function smoothly.
Lubricate the drive system: Check the drive belts, chains, and gears to see if they need lubrication. Add appropriate lubricants to reduce friction and prevent premature wear.
Lubricate bearings and sliding parts: For all bearings and sliding components, ensure they are adequately lubricated to keep the machine running smoothly.
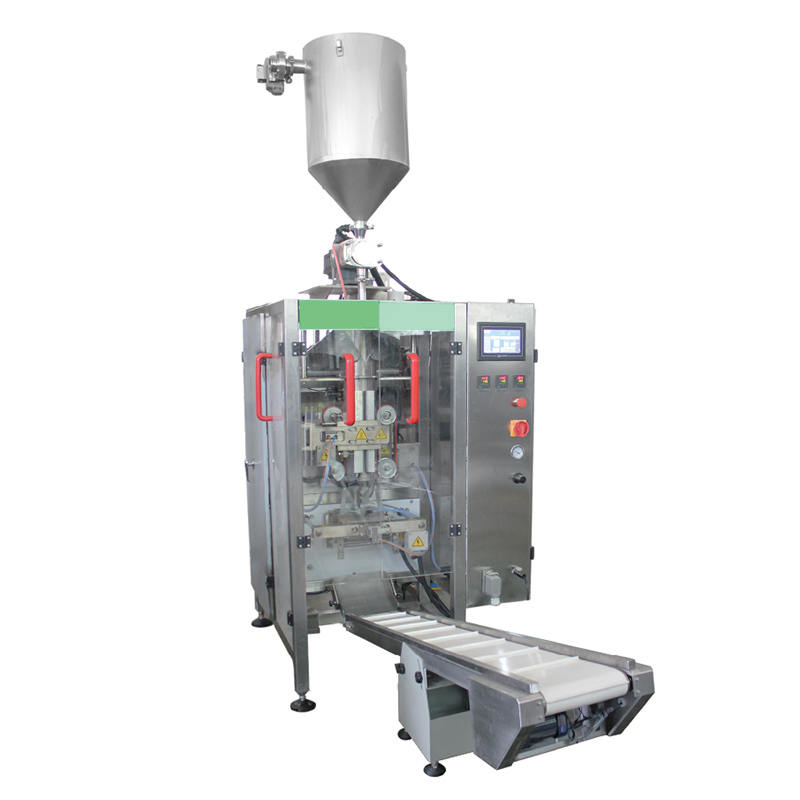
7. Inspect Pneumatic System (if applicable)
If the liquid packaging machine uses a pneumatic system to drive certain components, such as filling valves or sealing devices, daily checks of the pneumatic system are essential.
Check air pressure: Regularly check the air pressure in the pneumatic system to ensure it remains within the normal range. Low air pressure can lead to inaccurate filling or machine malfunctions.
Check air pipes and valves: Inspect air pipes and valves for any leaks to ensure the pneumatic system operates properly. Replace
any faulty parts immediately.
8. Record and Track Daily Maintenance
Keeping a record of daily maintenance is vital for equipment management. It helps track the maintenance history and allows for early detection of potential issues.
Maintenance logs: After each daily maintenance task, the operator should fill out a maintenance log to record the date, tasks completed, issues found, and actions taken.
Issue reporting: If any abnormalities or issues are found during maintenance, they should be reported to the maintenance team, and necessary repairs should be initiated.
9. Inspect Packaging Materials
The proper operation of the liquid packaging machine relies on high-quality packaging materials. Therefore, checking the packaging materials is also part of daily maintenance.
Inspect containers: Check the bottles, bags, or other containers used for packaging to ensure they are free of cracks or deformations. Any defects in the containers could lead to liquid leakage or packaging failures.
Inspect sealing materials: Check the packaging film and sealing components to ensure they are intact and functional, preventing liquid spillage during the sealing process.
Contact Us