In the design and use of powder packaging machines, the balance between accuracy and speed is a very important topic, because these two factors are usually contradictory. Too high speed may lead to reduced accuracy, while too high accuracy may reduce production efficiency. In order to achieve a balance between accuracy and speed, optimization is usually required from multiple aspects.
1. Automated control system
Modern powder packaging machines are usually equipped with advanced automated control systems (such as PLC systems), which can monitor and adjust various parameters in the packaging process in real time. Through automated control, the machine can optimize production efficiency by adjusting the filling speed and filling volume while ensuring packaging accuracy.
Intelligent monitoring: The filling volume and bag weight are monitored in real time through sensors, and the control system will adjust according to the feedback information to ensure the balance between packaging accuracy and speed.
Adjustment mechanism: The control system can automatically adjust the speed and filling volume according to the actual production situation, such as the weight deviation of the bag, so as to ensure the coordination of accuracy and speed.
2. Multi-level metering and precision control
Modern powder packaging machines usually adopt a multi-level metering system, which improves speed while ensuring accuracy through metering and adjustment at different stages. For example:
Coarse filling and fine filling: First, use a larger flow rate for coarse filling to quickly fill the powder into the packaging bag, and then fine-tune it through a fine metering device to ensure accuracy. This staged metering method can increase overall speed without sacrificing accuracy.
Feedback control system: Sensors can detect the amount of powder in each packaging bag. If any deviation is found, the system will immediately adjust the machine settings and make fine adjustments to ensure the packaging accuracy of each bag.
3. High-speed filling head and precision sensor
Powder packaging machines are often equipped with high-efficiency filling heads and precise sensors, which can accurately complete packaging tasks in a very short time.
Filling head design: The use of efficient filling head design can not only fill quickly, but also accurately control the amount of powder in each packaging bag. For example, some filling heads are equipped with vibration or pressurization devices to help powder flow evenly into the packaging bag, thereby improving accuracy.
Intelligent sensor feedback: Sensors can monitor the weight or volume of filling in real time and make rapid corrections to small errors in the packaging process, so as to avoid loss of accuracy while ensuring production speed.
4. Optimize material fluidity
The fluidity of powder directly affects the filling accuracy and speed. If the powder material is too sticky or has poor fluidity, the filling accuracy will be reduced and the filling process may be slow. In order to improve the accuracy while maintaining the speed, the following measures can be taken:
Improve the fluidity of powder: The fluidity of the material can be improved by adjusting the particle size, humidity or adding a flow agent, which can not only increase the filling speed but also ensure the accuracy of each bag of material.
Use vibration or fluidization device: By using technologies such as vibration equipment or fluidized bed to improve the fluidity of powder, reduce blockage and condensation, and ensure that the material can flow evenly into the packaging bag, thereby improving packaging efficiency and accuracy.
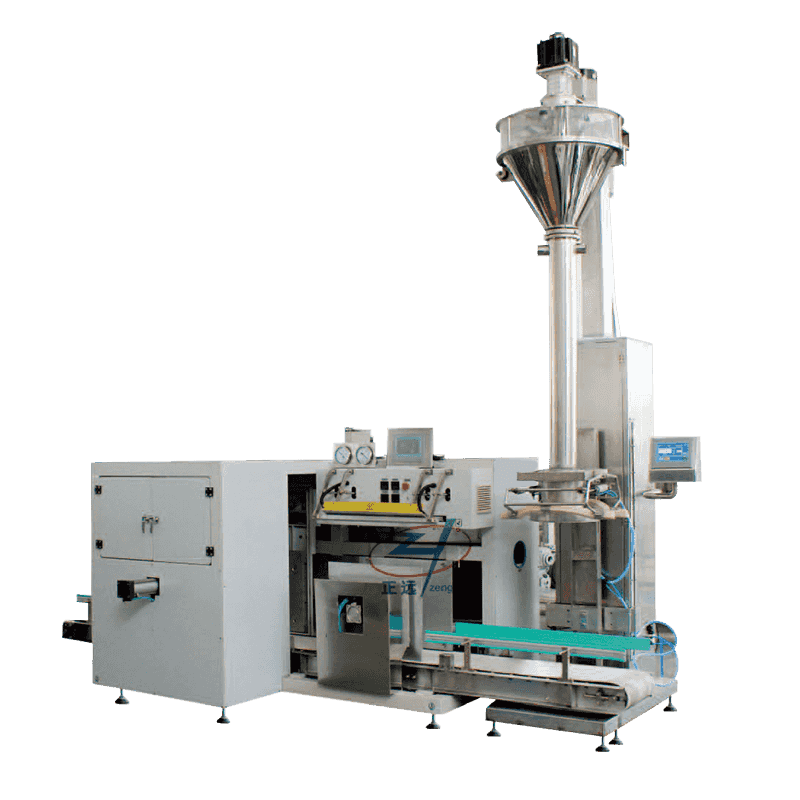
5. Mechanical structure and adjustment of the machine
The mechanical structure design of the powder packaging machine plays a key role in the balance between speed and accuracy. The following are some common design strategies:
Combination of high-speed motion and fine adjustment: The high-speed motion parts driven by servo motors are combined with a precise mechanical transmission system to ensure filling accuracy while maintaining high-speed operation.
Regular adjustment and calibration: The packaging machine needs to be calibrated regularly to ensure the accuracy of the filling head, metering system and sensor. If the accuracy of the packaging machine deviates, the machine can be corrected by manual or automatic adjustment.
6. Optimal configuration of packaging machine and production environment
Under different production environments, the optimal configuration of the packaging machine will also affect the balance between accuracy and speed. For example, in a humid environment or a high dust environment, the powder may absorb moisture or generate static electricity, affecting fluidity and filling accuracy. To solve these problems, the following measures can be taken:
Dehumidification equipment: Equipped with an air drying system to ensure that the powder maintains appropriate humidity during the packaging process to improve fluidity and accuracy.
Static protection: Use antistatic devices or select appropriate packaging bag materials to avoid the impact of static electricity on powder fluidity and filling accuracy.
7. Comprehensive analysis and optimization adjustment
By analyzing the entire process of packaging production, each link of the production line can be optimized to ensure the best balance between accuracy and speed. For example, analyze the bottlenecks of each link, optimize the inflow of materials, filling speed, sealing process, etc., to ensure efficient operation of each link.
Balancing accuracy and speed does not rely solely on the optimization of one aspect, but rather integrates multiple technical means, equipment configuration and operation management. By properly selecting the automatic control system, filling head design, material handling method, etc. of the powder packaging machine, the packaging speed can be increased without sacrificing packaging accuracy. With the advancement of intelligent and automated technology, the balance between accuracy and speed will become more flexible and efficient.
Contact Us