1. Heating Systems
Heating systems in liquid packaging machines are typically used to raise the liquid to the desired temperature. This is particularly important for high-viscosity liquids (such as oils, syrups, and sauces), as higher temperatures improve their flowability, making them easier to fill into packaging containers. Common heating methods include:
Electric heating elements: These directly heat the liquid, commonly found in small machines.
Heat exchangers: These systems indirectly heat the liquid by circulating hot water or steam, suitable for large-scale production.
2. Cooling Systems
Cooling systems are used to reduce the temperature of the liquid to the required level, particularly when dealing with heat-sensitive liquids like juices, milk, or pharmaceuticals. High temperatures can negatively affect the quality of the liquid (such as nutrient loss or flavor degradation). Cooling systems typically include:
Cooling coils: These are installed in the liquid’s path or container, using a cold water or ice water loop to lower the temperature.
Cooling fans/units: For some types of equipment, air-cooling systems can effectively lower the temperature of the machine or the liquid to prevent overheating.
Compressor refrigeration: Large machines may use compressor-based refrigeration systems to cool the liquid.
3. Temperature Sensors
Temperature sensors monitor the liquid's temperature in real-time, ensuring it stays within the preset ideal range. Common types of temperature sensors include:
Thermocouples: These sensors are accurate at measuring high temperatures and relay temperature data to the control system.
RTDs (Resistance Temperature Detectors): RTDs offer higher precision and are typically used in applications with stringent temperature control requirements, such as the pharmaceutical or food industries.
These sensors are usually placed at key locations along the liquid feed lines, heating or cooling systems to ensure accurate temperature readings.
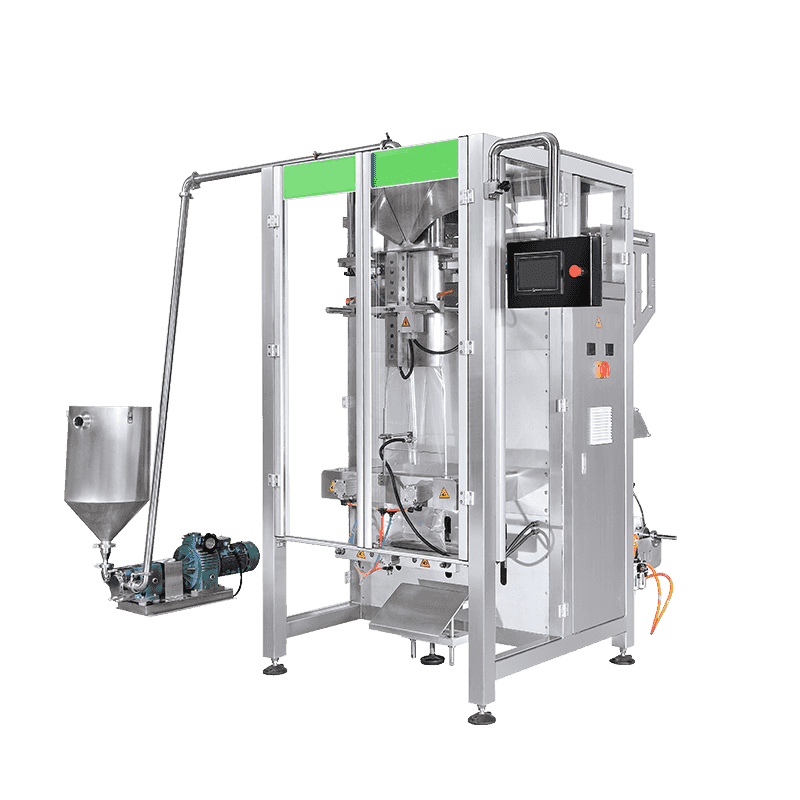
4. Temperature Control Valves and Regulation Systems
Temperature control valves are a central part of the temperature control system. Their role is to automatically adjust the heating or cooling process based on feedback from the temperature sensors. For example:
Automatic control valves: When sensors detect that the liquid temperature is too high, the control system will automatically open the cooling valve to increase the flow of cooling fluid. Conversely, if the temperature is too low, the heating process may be intensified.
Proportional control valves: These valves can adjust the flow rate of heating or cooling media based on real-time needs, allowing for fine control of the liquid temperature.
5. Temperature Controllers and PLC Systems
Temperature controllers are usually integrated with the packaging machine’s PLC (Programmable Logic Controller) system to form a closed-loop control system. If the liquid temperature deviates from the preset range, the PLC system immediately responds by adjusting the heating or cooling settings, ensuring the liquid temperature is quickly brought back to the ideal state. PLC systems typically have the following features:
High precision: They can fine-tune the liquid temperature through precise algorithms.
Programmable: Users can set different temperature control programs for different production stages (e.g., filling, sealing).
Alarms and fault diagnosis: When temperatures exceed the preset limits, the system can trigger alarms or even stop the machine, preventing defective products from being produced.
6. Thermal Protection and Automatic Adjustment
To prevent excessive heating or cooling from affecting the liquid, many temperature control systems also include thermal protection and automatic adjustment features. For example, the liquid packaging machine may have over-temperature protection, where the system will automatically stop heating or initiate cooling if the temperature goes too high, preventing overheating of the liquid. Additionally, the automatic adjustment feature can optimize the heating or cooling process based on the liquid's characteristics and environmental temperature changes, improving overall production efficiency.
7. Handling Temperature Variations in Different Liquids
Different types of liquids respond differently to temperature fluctuations, so the temperature control system is often optimized for specific liquid properties. For example:
Low-viscosity liquids (such as water, beverages): These liquids flow easily, so temperature fluctuations have less impact on their processing.
High-viscosity liquids (such as sauces, syrups): These liquids become more viscous at lower temperatures, so the temperature control system needs to heat the liquid to improve flowability.
Heat-sensitive liquids (such as milk, pharmaceuticals): These require stringent temperature control to avoid the loss of nutrients or active ingredients due to overheating.
8. Smart Temperature Control Systems
With the advancement of technology, some high-end liquid packaging machines now feature smart temperature control systems. Through IoT (Internet of Things) technology, the equipment can continuously collect temperature data and analyze it on cloud platforms, helping users optimize temperature management, improve energy efficiency, and conduct remote diagnostics or troubleshooting. These systems can automatically adjust temperature control for different production batches, providing full automation in temperature management.
Contact Us